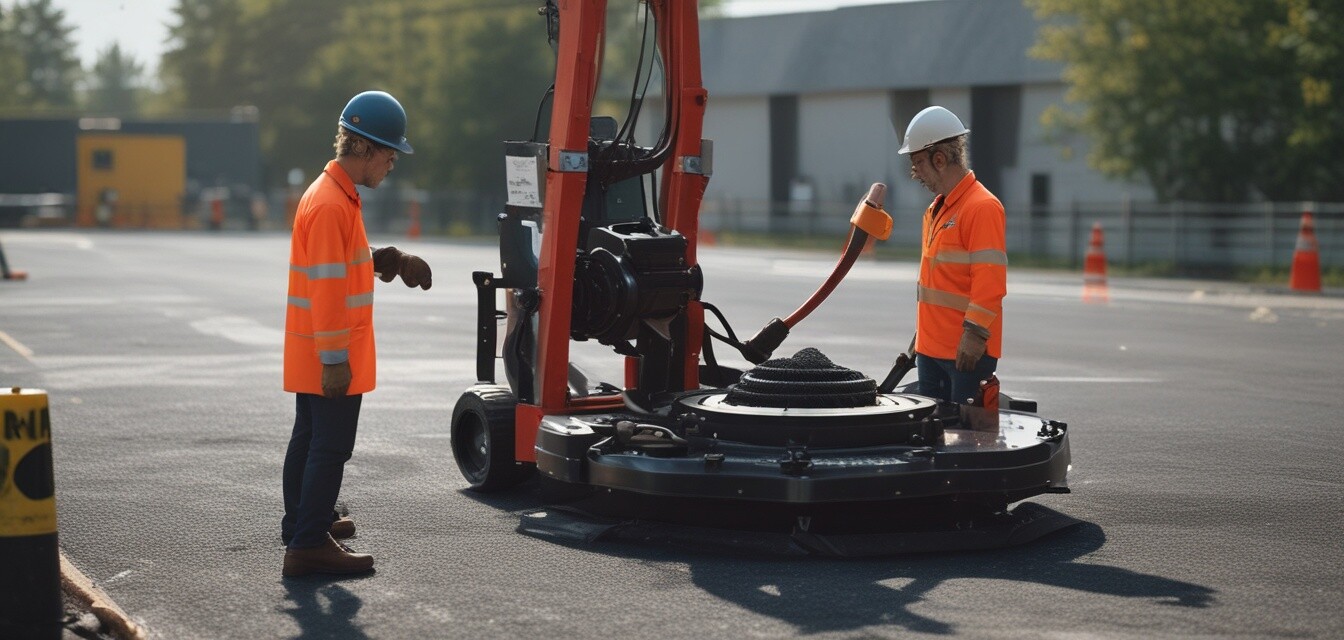
Best practices for asset management in asphalt paving
Key Takeaways
- Maintain your asphalt paving equipment regularly to ensure long-lasting performance.
- Effective supply management strategies help reduce costs and streamline operations.
- Implementing tracking systems enhances the visibility of equipment utilization.
- Prioritize staff training to maximize the efficiency of asset use.
- Evaluate equipment budgets for better financial planning in asphalt projects.
Managing asphalt paving assets is crucial for ensuring efficiency and effectiveness in your paving projects. Whether you're a contractor, a DIY enthusiast, or a property owner, understanding best practices in asset management can lead to significant cost savings and improved project outcomes. This guide will explore essential strategies for maintaining equipment, managing supplies, and optimizing operations within the asphalt paving niche.
1. Importance of equipment maintenance
Regular maintenance is key to prolonging the life of your asphalt paving equipment. A well-maintained machine not only performs better but also reduces the risk of unexpected breakdowns that can cause project delays. Here are some maintenance tips:
- Establish a routine maintenance schedule based on usage.
- Perform daily inspections before each job.
- Keep equipment clean to prevent wear and tear.
- Replace worn-out parts promptly to avoid further damage.
Creating a maintenance checklist
A maintenance checklist can help keep track of tasks. Consider the following sections in your checklist:
Task | Frequency | Notes |
---|---|---|
Inspect hydraulic levels | Weekly | Ensure levels are within the recommended range. |
Check engine oil | After every 50 hours | Change oil every 100 hours of use. |
Clean air filters | Monthly | Replace if heavily soiled. |
Inspect tires for wear | Weekly | Replace tires that are significantly worn. |
2. Effective supply management
Good supply management is essential for keeping your asphalt paving projects on time and within budget. Implementing solid buying practices can help ensure that you have the right materials, at the right time. Here are some supply management strategies:
- Establish relationships with reliable suppliers.
- Track inventory levels to avoid shortages or excess.
- Take advantage of bulk purchasing to reduce costs.
- Assess material quality regularly to meet project standards.
Using inventory management software
Investing in inventory management software can enhance your ability to track and manage supplies efficiently. Key features to look for include:
- Real-time inventory tracking
- Alerts for low stock levels
- Order history tracking
- Integration with accounting software
3. Implementing asset tracking systems
Asset tracking systems can simplify identifying and monitoring your paving equipment. Knowing where equipment is located and its condition can optimize your operations significantly. Here’s how to set up an effective asset tracking system:
- Use GPS tracking for equipment location.
- Implement RFID tags or barcodes for easy inventory checks.
- Log equipment usage to maintain performance data.
- Evaluate utilization rates to identify underused assets.
4. Prioritizing staff training
Investing in your workforce is vital for maximizing the efficiency of your equipment. Training ensures that all staff members are well-versed in using equipment correctly and safely. Consider the following approaches:
- Conduct regular training sessions on equipment operation.
- Encourage feedback from employees on training needs.
- Utilize online resources and courses for continuous learning.
- Incorporate safety protocols into training programs.
5. Budget evaluation and financial planning
Financial planning is necessary for maintaining a sustainable operation. Regularly evaluating your equipment and supply budgets can guide strategic investment decisions. Tips for budget evaluation include:
- Review past project costs to identify savings opportunities.
- Allocate funds for unexpected repairs or upgrades.
- Prioritize essential equipment purchases over nice-to-haves.
- Conduct a return-on-investment analysis for new tools or machinery.
Pros
- Well-maintained equipment performs better and lasts longer.
- Good supply management can significantly reduce costs.
- Effective tracking enhances visibility and accountability.
- Staff training leads to safer work environments and higher efficiency.
- Budget evaluations foster strategic financial planning.
Cons
- Initial investment in systems and software can be high.
- Training requires time that could be spent on projects.
- Dependence on technology may create hurdles during system failures.
- Managing relationships with suppliers requires effort and time.
- Tracking systems can be cumbersome without proper training.
Conclusion
Implementing best practices in asset management is essential for any asphalt paving operation. Regular maintenance, effective supply management, tracking systems, staff training, and budget evaluations all play a crucial role in achieving efficient and cost-effective project outcomes. By following these guidelines, contractors, DIY enthusiasts, and property owners can ensure successful paving projects and make informed investment choices. For more resources on asphalt paving, check out our buying guides and explore different paving tools to elevate your projects.